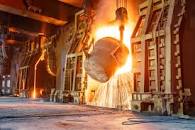
Steel Melt Shop Practice…
There are two main types of steel melting shops: the electric arc furnace (EAF) and the basic oxygen furnace (BOF). The EAF utilizes an electric arc to melt and refine steel scrap, resulting in a more flexible and energy-efficient process. On the other hand, the BOF relies on blowing oxygen through a vessel containing molten iron, allowing impurities to be oxidized and removed. This method is particularly suitable for producing large quantities of steel at a lower cost. While both processes have their advantages and disadvantages, the choice between them depends on various factors such as the desired steel quality, production volume, and availability of raw materials. Therefore, understanding the technological differences between the EAF and BOF is crucial for determining the most suitable steel melting shop for a specific application.
Electric Arc Furnace (EAF)…
An electric arc furnace (EAF) is a type of furnace that uses high-intensity electric arcs to melt and refine metallic ores. The process begins by loading scrap metal into the furnace, which is then subjected to an electric current. The current creates an arc between the electrodes and the metal, generating intense heat that melts the scrap. The molten metal is then refined and the impurities are removed before it is poured into molds to form new products. One advantage of EAFs is their ability to quickly melt and process a wide range of metals, including steel and iron. Additionally, EAFs are considered more environmentally friendly compared to traditional furnaces as they emit fewer greenhouse gases. However, one disadvantage is the high energy consumption associated with EAFs, making them more expensive to operate.
Basic of Operation and Maintenance …
The basic operation and maintenance of an electric arc furnace encompasses several important tasks. Firstly, to commence the operation, the furnace needs to be preheated to the desired temperature using the available heating elements. Once the furnace is ready, the raw materials, such as scrap metal and fluxes, are charged into the furnace through a designated charging system. The electric current is then passed through graphite electrodes, creating an intense arc that melts the materials. During the melting process, it is crucial to monitor various parameters like temperature, chemical composition, and power consumption to ensure optimal performance. Additionally, regular maintenance of the furnace involves inspecting and replacing damaged or worn-out electrodes, refractory lining, and cooling systems. Adequate maintenance practices guarantee the safe and efficient functioning of the electric arc furnace, which is essential for the production of high-quality steel and other metal alloys.
Basic Oxygen Furnace (BOF)…
The basic oxygen furnace (BOF) is a type of steelmaking furnace that operates by blowing oxygen onto a hot metal bath to remove impurities and convert the molten iron into steel. This process is known as the basic oxygen process (BOP) and is widely used in the steel industry. The advantage of using a BOF is its high production capacity and the ability to produce high-quality steel. The BOF also allows for the use of a wide range of raw materials, including scrap steel, which makes it cost-effective. However, one of the main disadvantages of the BOF is its high energy consumption. It also produces a large amount of waste gas and solid waste, which can have negative environmental impacts if not properly managed. Overall, the BOF is an important tool in steel production, but its drawbacks need to be taken into consideration for sustainable manufacturing.
Basic of operation and Maintenance…
Basic oxygen furnace (BOF) is a crucial component in the steelmaking process. Its operation and maintenance are essential to ensure the production of high-quality steel. The BOF is primarily used to convert molten iron into steel by blowing oxygen through the molten metal. During operation, the furnace must be continuously monitored to maintain the desired temperature and chemical composition. Regular maintenance is required to keep the furnace in optimal condition, including checking and replacing refractory lining, inspecting and repairing gas and oxygen supply systems, and cleaning the furnace internals. Additionally, proper handling of waste materials generated during the process is necessary to maintain environmental standards. Overall, understanding the basic operation and implementing routine maintenance procedures is vital to maximize the efficiency and longevity of a basic oxygen furnace.