Silico and Ferro manganese in Steel Making
Silico and ferro manganese are two types of ferroalloys used in the steelmaking process. They serve as sources of manganese, which is an essential element in steel production due to its properties that enhance the strength, hardness, and wear resistance of steel.
Silico Manganese
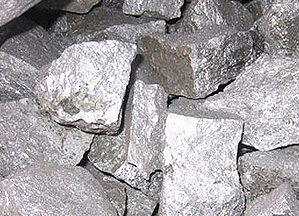
Silico manganese, an alloy of manganese, silicon, and iron, is primarily used as a deoxidizer and alloying agent, contributing to the reduction of Sulphur and oxygen in steel. Its typical composition includes 60-70% manganese, 10-30% silicon, and 1-3% carbon. The presence of silicon makes it particularly effective in improving the tensile strength and ductility of steel, making it suitable for producing structural steel, stainless steel, and high-strength low-alloy steel.
Composition:
- Manganese (Mn): 60-70%
- Silicon (Si): 10-30%
- Carbon (C): 1-3%
Applications:
- Deoxidizer: Silico manganese acts as a deoxidizer, removing oxygen from molten steel, thus preventing the formation of undesirable oxides.
- Desulfurizer: It helps in reducing the Sulphur content in steel, improving its quality and mechanical properties.
- Alloying Element: Enhances the strength, hardness, and wear resistance of steel, especially in the production of structural steel, stainless steel, and tool steel.
Ferro Manganese
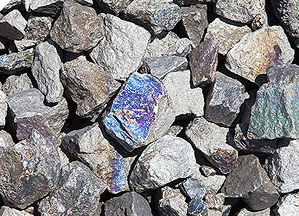
Ferro manganese is an alloy with 65-90% manganese and 6-8% carbon, used to increase the hardness and wear resistance of steel. It serves as a crucial deoxidizing agent and is vital in manufacturing high-carbon steel and cast iron. The production processes for these alloys involve the smelting of manganese ore in submerged electric arc furnaces, where reduction reactions occur in the presence of carbon sources such as coke or coal.
Composition:
- Manganese (Mn): 65-90%
- Carbon (C): 6-8%
- Silicon (Si): 0.2-1%
Applications:
- Deoxidizer: Like silico manganese, ferro manganese is also used to remove oxygen from steel.
- Alloying Element: It increases the tensile strength and hardness of steel. It is commonly used in the production of carbon steel, stainless steel, and low-alloy steel.
- Carbon Content Control: The high carbon content in ferro manganese makes it suitable for adjusting the carbon levels in steel, especially in the production of high-carbon steel and cast iron.
Major Differences
- Silicon Content: Silico manganese contains a significant amount of silicon, which is not present in ferro manganese. This makes silico manganese more effective as a deoxidizer.
- Carbon Content: Ferro manganese has a higher carbon content compared to silico manganese, making it suitable for applications where increased carbon levels are required.
- Applications: While both are used for deoxidation and alloying, the presence of silicon in silico manganese makes it more effective in certain steelmaking processes, such as the production of steel grades that require lower carbon and sulfur levels.
- Cost and Availability: Silico manganese is generally more cost-effective than ferro manganese due to its dual role as a deoxidizer and alloying element.
Determining the desired quantity
Determining the desired quantity of silico manganese (SiMn) to be used in the steelmaking process depends on several factors, including the type of steel being produced, the target chemical composition, and the specific roles of silico manganese as a deoxidizer and alloying element. Here are the key considerations:
1. Steel Grade and Specification
- Target Composition: Identify the desired chemical composition of the steel, particularly the manganese and silicon content.
- Standards and Specifications: Follow industry standards and specifications (such as ASTM, DIN, or JIS) that define the required composition for specific steel grades.
2. Function of Silico Manganese
- Deoxidation: Silico manganese is added to remove oxygen from molten steel. The amount needed depends on the initial oxygen content and the desired deoxidation level.
- Alloying: To achieve the required manganese and silicon levels, consider how much silico manganese is needed to reach these targets.
3. Furnace Type and Process
- Type of Furnace: Different furnace types (e.g., electric arc furnace, basic oxygen furnace) have varying efficiency levels and may require different SiMn quantities.
- Process Parameters: Temperature, time, and slag composition affect the reaction efficiency and thus the quantity of SiMn required.
4. Raw Material Quality
- Composition of Raw Materials: Analyze the initial composition of the raw materials to determine how much additional manganese and silicon are needed.
- Impurities: Consider impurities in the raw materials that may affect the efficiency of SiMn additions.
5. Calculation of Additions
To calculate the necessary quantity of silico manganese, you can use the following approach:
Step 1: Determine Required Additions
- Target Manganese and Silicon Content: Establish the desired manganese and silicon content in the final steel.
- Current Manganese and Silicon Levels: Measure the existing levels in the molten steel before adding SiMn.
Step 2: Calculate Addition Rate

- Steel Weight: Calculate the total weight of the steel batch.
- Mn% in SiMn: The manganese content in SiMn (typically 60-70%).
- Si% in SiMn: The silicon content in SiMn (typically 10-30%).
Step 3: Adjust for Process Efficiency
- Yield Losses: Consider potential losses during the process, which might necessitate adjusting the calculated SiMn addition upwards to ensure the target composition is achieved.
- Overhead Adjustments: Factor in any overhead adjustments for variations in furnace conditions or raw material quality.
6. Economic Considerations
- Cost of Silico Manganese: Consider the cost implications of using different quantities of SiMn.
- Cost-Effectiveness: Balance the need for alloying with the overall cost of production.
Example Calculation
Suppose you have 1000 kg of molten steel with an initial manganese content of 0.5% and you want to increase it to 1.5%. Assuming silico manganese contains 65% manganese:
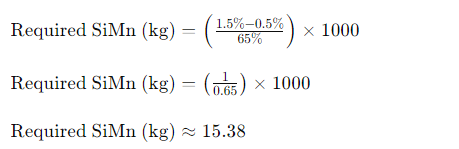
Thus, approximately 15.38 kg of silico manganese would be needed to achieve the desired manganese content.
By considering these factors and performing the necessary calculations, you can determine the optimal quantity of silico manganese to add to the steelmaking process.
Overall Impact on Steel Technology
- Enhanced Steel Properties: The use of silico manganese and ferro manganese leads to steel with superior mechanical properties, including increased strength, toughness, and wear resistance.
- Improved Product Quality: By reducing impurities and controlling chemical compositions, these ferroalloys contribute to higher-quality steel products.
- Innovation and Efficiency: The ability to produce advanced steel grades with specific properties has driven innovation in steel technology, allowing for the development of new applications and more efficient production processes.
Strategic considerations in choosing between silico manganese and ferro manganese.
When selecting between silico manganese and ferro manganese for steelmaking, several strategic considerations come into play. These considerations involve evaluating the specific requirements of the steel being produced, the desired properties of the final product, cost factors, and environmental impacts. Here are the key strategic considerations:
1. Desired Manganese Content
- Silico Manganese: Contains 60-70% manganese, which is ideal for applications where both manganese and silicon are required in significant amounts.
- Ferro Manganese: Contains a higher manganese content of 65-90%, suitable for applications where manganese is the primary requirement and silicon is less critical.
2. Silicon Content and Its Impact
- Silico Manganese: The presence of 10-30% silicon makes it an effective deoxidizer and desulfurizer, particularly beneficial for producing low-sulfur and low-carbon steel grades.
- Ferro Manganese: Has low silicon content, typically 0.2-1%, and is used when silicon additions need to be minimized or when steel requires higher carbon content.
3. Carbon Content Control
- Silico Manganese: With 1-3% carbon, it is suitable for producing steels with controlled carbon levels, such as high-strength low-alloy steels.
- Ferro Manganese: Higher carbon content (6-8%) makes it suitable for adjusting the carbon levels in high-carbon steel or cast iron production.
4. Cost Considerations
- Silico Manganese: Often more cost-effective due to its dual role as a deoxidizer and alloying agent. It may reduce overall alloy costs when both manganese and silicon are needed.
- Ferro Manganese: May be more expensive due to higher manganese content but is necessary when the specific steel grade requires minimal silicon.
5. Production Process Requirements
- Silico Manganese: Suitable for processes where simultaneous deoxidation and alloying are required, especially in electric arc furnace operations.
- Ferro Manganese: Used in processes where precise control of manganese and carbon content is essential, often in basic oxygen furnaces.
6. Environmental and Efficiency Considerations
- Silico Manganese: Offers benefits in terms of reducing emissions and energy consumption due to its lower carbon content and effective deoxidation.
- Ferro Manganese: Requires careful management of emissions, especially carbon emissions, due to higher carbon content.
7. Mechanical Properties of Final Steel
- Silico Manganese: Enhances tensile strength, ductility, and corrosion resistance, making it suitable for structural, automotive, and stainless steel applications.
- Ferro Manganese: Increases hardness and wear resistance, ideal for high-carbon steels used in tools, rails, and other heavy-duty applications.
8. Availability and Supply Chain
- Silico Manganese: The availability of manganese and silicon sources can influence the choice, especially if silicon is also a significant requirement in other steel production processes.
- Ferro Manganese: May be preferred in regions with abundant manganese resources and limited silicon, ensuring a stable supply chain.