Meta TechX Engineers:
In the world of manufacturing and industrial processes, TPM stands for Total Productive Maintenance. It is a method that focuses on the proactive and planned maintenance of machinery and equipment. TPM aims to maximize productivity, reduce downtime, and improve the overall efficiency of the production process. In this article, we will explore what TPM is in the context of the hot rolling process, how it works, and the advantages it offers. Meta Blogs
What is TPM in the Hot Rolling Process?
TPM in the hot rolling process refers to the application of Total Productive Maintenance principles to the machinery and equipment used in the rolling of metal at high temperatures. Hot rolling is a critical stage in the production of steel and other metal products. It involves shaping and forming metal by passing it through a series of rolling mills, which apply pressure and temperature to transform the raw material into the desired shape.
How Does TPM Work in the Hot Rolling Process?
TPM in the hot rolling process involves a systematic approach to equipment maintenance that focuses on the prevention of breakdowns and the optimization of performance. Here are the key steps involved in implementing TPM:
- Identification and Documentation: The first step is to identify all the equipment and machinery used in the hot rolling process. These should be documented along with their critical parameters, maintenance requirements, and history.
- Autonomous Maintenance: Operators are trained to take ownership of routine maintenance tasks such as cleaning, lubricating, and inspecting equipment. This empowers them to detect early signs of wear or malfunction and take necessary actions.
- Preventive Maintenance: Scheduled maintenance activities are performed based on the manufacturer’s recommendations and past performance data. This includes periodic inspections, adjustments, and replacements to prevent unexpected breakdowns.
- Predictive Maintenance: By analyzing real-time data collected from sensors and monitoring systems, potential failure patterns can be identified. Predictive maintenance allows for the proactive replacement of parts before they fail, minimizing downtime.
- Continuous Improvement: TPM fosters a culture of continuous improvement by encouraging operators and maintenance personnel to suggest and implement ideas for optimizing equipment performance and reliability.
Advantages of TPM in the Hot Rolling Process
Implementing TPM in the hot rolling process offers several advantages that contribute to increased productivity and efficiency. Here are some of the key benefits:
- Reduced Downtime: By proactively maintaining equipment, TPM helps minimize unexpected breakdowns and reduces downtime associated with repairs. This enables a smooth and uninterrupted production flow.
- Improved Quality: Proper maintenance ensures that equipment operates within specified parameters, leading to better product quality and fewer defects. TPM helps to standardize processes and eliminate variations that can impact product consistency.
- Increased Equipment Life: Regular maintenance and timely replacements help extend the lifespan of equipment, reducing the need for costly replacements. This improves the return on investment and lowers overall production costs.
- Higher Overall Equipment Efficiency (OEE): TPM aims to maximize the OEE of equipment by addressing factors such as availability, performance, and quality. This results in increased production output and improved utilization of resources.
- Enhanced Safety: The proactive nature of TPM helps identify potential safety hazards and take corrective actions before accidents occur. By maintaining equipment in optimal condition, the risk of work-related injuries is significantly reduced.
Conclusion
TPM in the hot rolling process is a powerful tool for improving the productivity, efficiency, and reliability of machinery and equipment used in the rolling of metal at high temperatures. By implementing TPM principles, manufacturers can optimize the performance of their equipment, reduce downtime, improve product quality, and ultimately achieve higher levels of productivity and profitability. Embracing TPM is not only a sound maintenance strategy but also a key driver for success in the competitive world of manufacturing.
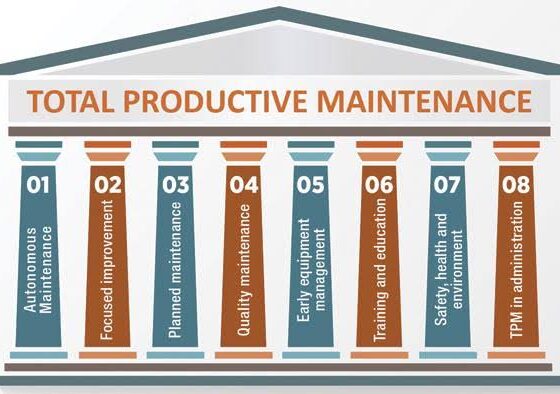