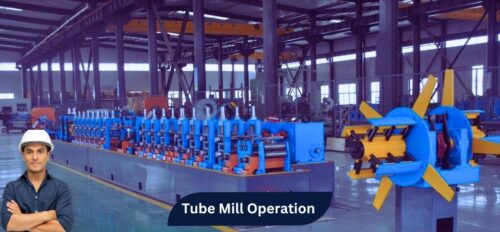
ERW Tube: Overview
ERW (Electric Resistance Welded) tube is a type of steel pipe manufactured through a process in which a flat steel strip is shaped into a tubular form and welded along its longitudinal seam using electric resistance welding. ERW tubes are widely used in various industries, such as construction, automotive, agriculture, and energy, due to their cost-effectiveness, uniformity, and strength.
Characteristics of ERW Tubes
- High Precision: Uniform wall thickness and smooth surface.
- Strength: The welded seam has strength comparable to the parent metal.
- Cost-Effective: Economical production process.
- Versatility: Available in various sizes, thicknesses, and grades.
- Applications: Structural pipes, scaffolding, water and gas pipelines, and automotive components.
ERW Tube-Making Process: Step-by-Step
The ERW tube-making process can be divided into several steps, starting from raw material preparation to final finishing.
1. Raw Material Preparation
- Steel Coils: High-quality steel coils are used as the raw material. The steel grade depends on the required tube specifications.
- Uncoiling: The steel coil is unrolled and fed into the production line.
- Shearing and End Welding: The coil ends are cut and welded together to ensure continuous feeding into the mill.
2. Edge Preparation
- Slitting: The steel strip is slit into the required width based on the tube diameter.
- Edge Trimming: Ensures smooth and uniform edges to prevent welding defects.
3. Forming
- Roll Forming:
- The steel strip is passed through a series of forming rolls.
- These rolls gradually bend the flat strip into a circular or desired tubular shape.
4. Electric Resistance Welding (ERW)
- Principle of ERW:
- High-frequency electric current (AC or DC) is passed through the edges of the tube, generating heat through resistance.
- The heat melts the edges, and they are pressed together to form a strong, seamless weld.
- Welding Process:
- No filler material is used.
- The welding area is precisely controlled to ensure a smooth and strong seam.
5. Weld Bead Removal
- Internal and External Bead Trimming:
- Excess weld material (bead) is removed from the inner and outer surfaces of the tube.
- This ensures a smooth finish and improves dimensional accuracy.
6. Sizing and Shaping
- Sizing Rolls:
- The welded tube passes through sizing rolls to achieve the desired dimensions.
- Circular tubes can be shaped into square, rectangular, or other profiles during this step.
7. Heat Treatment (Optional)
- Post-Weld Heat Treatment (PWHT):
- Some tubes undergo heat treatment to relieve stress, improve mechanical properties, and ensure weld integrity.
- Typically required for high-pressure or structural applications.
8. Straightening
- Straightening Machines:
- Ensure the tube is perfectly straight and free from bends or distortions.
- Critical for structural and precision applications.
9. Cutting
- Length Cutting:
- Tubes are cut to the required lengths using rotary saws or flying saws.
- Precision cutting ensures uniform lengths.
10. Surface Treatment
- Pickling and Coating:
- Tubes may be pickled to remove surface scale or rust.
- Coatings such as galvanizing, painting, or powder coating can be applied for corrosion resistance.
- Deburring:
- Removes sharp edges and burrs from the cut ends.
11. Inspection and Testing
- Non-Destructive Testing (NDT):
- Ultrasonic or Eddy Current Testing ensures weld integrity.
- Dimensional Inspection:
- Checks diameter, thickness, length, and other parameters.
- Mechanical Testing:
- Tests for tensile strength, hardness, and elongation.
- Hydrostatic Testing:
- Ensures the tube can withstand specified pressures without leakage.
12. Bundling and Packing
- Bundling:
- Finished tubes are bundled together for easy handling and transportation.
- Marking and Labeling:
- Each tube is marked with details like size, grade, and batch number for traceability.
- Packing:
- Tubes are packed in protective covers to prevent damage during transportation.
Advantages of ERW Tubes
- Cost-Effective Production: High-speed, automated process reduces production costs.
- Customizability: Can be produced in a wide range of sizes and profiles.
- Strength and Durability: Weld seam is as strong as the base material.
- Versatility: Suitable for various industrial, structural, and automotive applications.
- Smooth Finish: Excellent surface quality due to precise manufacturing and bead removal.
Applications of ERW Tubes
- Structural: Scaffolding, building frames, and bridges.
- Automotive: Exhaust systems, chassis, and structural components.
- Energy: Pipelines for oil, gas, and water.
- Furniture: Chair frames and other tubular furniture.
- Agriculture: Irrigation systems and fencing.
Maintenance and Quality Assurance
- Machine Maintenance: Regular inspection and maintenance of rollers, welding equipment, and cutting tools.
- Raw Material Quality: Ensure consistent quality of steel coils for reliable production.
- Weld Monitoring: Continuous monitoring of welding parameters (current, voltage, pressure).
- Surface Finish Control: Regular cleaning of bead trimming tools and coating systems.
The ERW process provides a high-efficiency, cost-effective method for producing high-quality steel tubes, meeting the diverse demands of industries worldwide.
Tags: Meta TechX, Meta TechX Engineers, Tube Mill